top of page

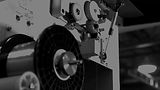
Wire EDM
With 8 4&5-Axis Wire EDM Machines and one of the largest submersible tanks in North America, we can handle a wide range of sizes and shapes

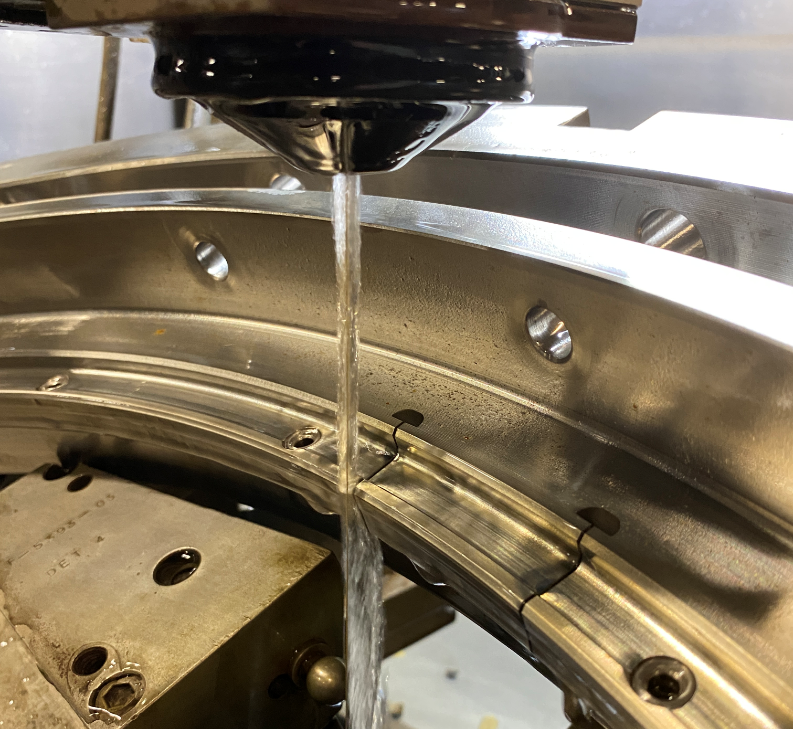
Hi-Tek Manufacturing has decades of experience with Wire EDM and has been at the forefront of utilizing the latest technology in machines in this process. As a result, Hi-Tek's Wire EDM Processes can cut various shapes into parts that can't be achieved through other types of machining, and can do so quickly and accurately. We have a total of 8 Wire EDM machines. This, along with having one of the largest submerged tanks in North America, gives Hi-Tek the capability of machining a wide range of sizes and shapes.

bottom of page